Accelerating Innovation in GearBox Systems Using Digital Twins

Company
Private Limited
Domain
Product Manufacturer
Service
Product Validation, Asset performance
Technology
CAE Tools
Problem Statement
Developing efficient gear Box is a challenging task as it involves intricate interactions between components like shafts, bearing, and gears. Traditional methods struggle to:
- Simulate dynamic interactions under diverse operating conditions.
- Validate corrective actions before applying changes to critical components
- Optimize designs for next-gen engineers, without extensive physical prototyping.
Solution
Digital Twin Framework for Gearbox Systems
- A virtual representation of the entire Gearbox, including shafts, bearing, and gear systems. They contain various phases such as Data acquisition, Data processing, Condition assessment, Diagnostic and Decision analytics
- Models real-world performance across various operating load conditions and environmental factors.
- Integrates IoT sensor data to provide real-time updates and predictive insights for wear, efficiency, and performance.
- Utilizes data models to refine simulations of gearbox dynamics, load management, and energy efficiency.
- Enhances decision-making with predictive analytics insights leads to better decision making
Impact/Benefits to the Customer
- Remote asset monitoring outcome supports the customer to take JIT decision and reduce cost.
- Simulations capture detailed Gearbox behaviour under various loads, speeds, and conditions, enabling engineers to identify optimization opportunities early
- Reduces reliance on physical prototyping and field testing, saving significant time and development costs.
Accelerating Innovation in GearBox Systems Using Digital Twins
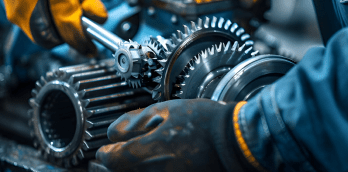
Company
Private Limited
Domain
Product Manufacturer
Service
Product Validation, Asset performance
Technology
CAE Tools
Problem Statement
Developing efficient gear Box is a challenging task as it involves intricate interactions between components like shafts, bearing, and gears.
Traditional methods struggle to:
- Simulate dynamic interactions under diverse operating conditions.
- Validate corrective actions before applying changes to critical components
- Optimize designs for next-gen engineers, without extensive physical prototyping.
Solution
Digital Twin Framework for Gearbox Systems
- A virtual representation of the entire Gearbox, including shafts, bearing, and gear systems. They contain various phases such as Data acquisition, Data processing, Condition assessment, Diagnostic and Decision analytics
- Models real-world performance across various operating load conditions and environmental factors
- Integrates IoT sensor data to provide real-time updates and predictive insights for wear, efficiency, and performance.
- Utilizes data models to refine simulations of gearbox dynamics, load management, and energy efficiency.
- Enhances decision-making with predictive analytics insights leads to better decision making
Impact/Benefits to the Customer
- Remote asset monitoring outcome supports the customer to take JIT decision and reduce cost.
Simulations capture detailed Gearbox behaviour under various loads, speeds, and conditions, enabling engineers to identify optimization opportunities early.
Reduces reliance on physical prototyping and field testing, saving significant time and development costs.
- Simulations capture detailed Gearbox behaviour under various loads, speeds, and conditions, enabling engineers to identify optimization opportunities early.
- Reduces reliance on physical prototyping and field testing, saving significant time and development costs.
Ready to transform your
business with cutting-edge
software solutions?
Let’s connect and explore
how our expertise can elevate your business